با بهکارگیری مواد اولیه و مفاهیم بستهبندی متفاوت، تولیدکنندگان میتوانند به خوبی پاسخگوی نیازهای بازار مرتبط با راهکارهای بستهبندی پایدار باشند.
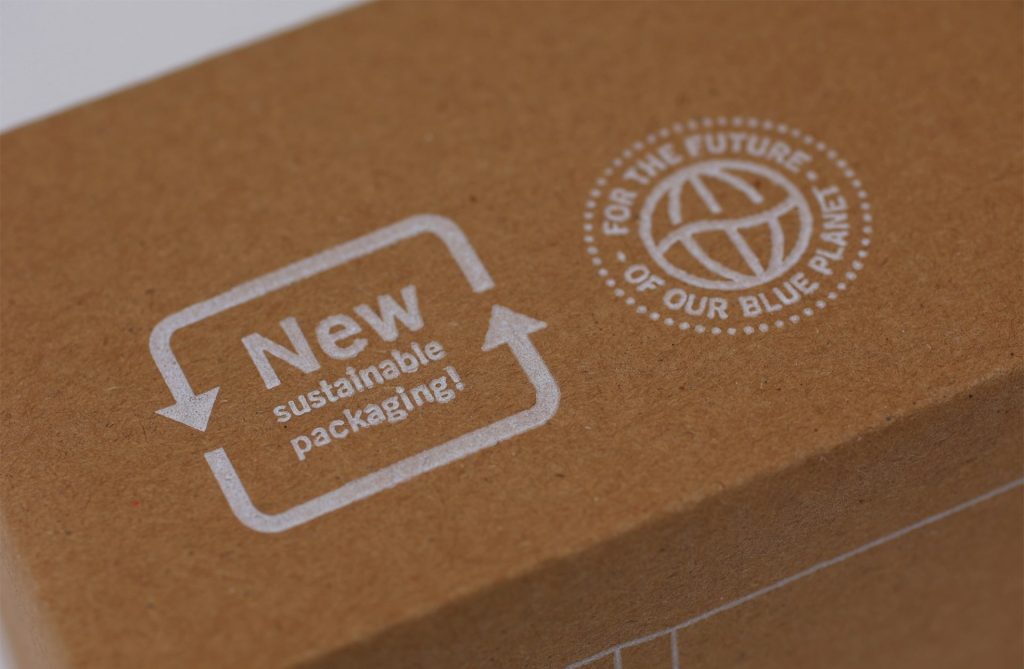
قوانین جدید بستهبندی از سال 2019 در کشور آلمان به سرعت در حال تصویب هستند. در کنار سایر مسایل، بازیافت مواداولیه و قابلیت استفاده مجدد از بستهها، سهم عمدهای را به خود اختصاص دادهاند. معرفی سیستمهای کاربردی باز و بستهشدن چند باره بستهبندیها درکنار اینکه پلاستیکها قابل استفاده مجدد و در نتیجه منبعی ارزشمند هستند، گاهی مهم در جهتی صحیح است. موازی با این، صنعت بستهبندی در مسیر انتخاب جایگزینهایی برای مواداولیه فعلی هستند. علاوه بر معرفی سیستم چرخه بسته برای پلاستیکها، کاهش مصرف پلاستیکها در تولید بستهبندی، خبر از نگرشی محسوس دیگر برای ارتقای پایدار صنعت بستهبندی میدهد.
امروز بستهبندیهای پلاستیکی، حدود 60درصد از ضایعات کلی بستهبندیها را به خود اختصاص دادهاند. در سطح جهانی حدود 325میلیون تن پلاستیک هر سال فرآیند میشوند که از آنها حدود 80 میلیون تن برای بستهبندیهای پلاستیکی مورد استفاده قرار میگیرند در مکانهایی همچون اروپا، آسیا و امریکا.
تولید انواع پلاستیک در حال افزایش است. تخمین زده میشود که تولید جهانی پلاستیکها در دو دهه آینده دو برابر شود.
بستههای پلاستیکی البته مزیتهای بسیاری دارند بهویژه در صنعت غذا. با افزودن لایههای مختلف پلیمری، میتوان به ترکیبهای جدید پلاستیکی رسید که بهطور خاص در جهت افزایش نفوذناپذیری برای مراقبت از محصولات درونشان طراحی شدهاند. مواد اولیه پلاستیکهای حرارتی، قابلیتهای خوبی در طراحی و شکل بستهها دارند. علاوه بر این، بستههای پلاستیکی محافظت بسیار خوبی از کالا در چرخه لجستیک انجام میدهند. همچنین ایمنی آنها را برای مصرفکننده تضمین میکنند. به خاطر نقش مثبت پلاستیکها در افزایش عمر محصولات غذایی، بستهبندیهای پلاستیکی نقشی مهم در کاهش ضایعات غذایی خواهند داشت.
رویکرد جامع برای یافتن راهکاری موثر
در راستای اجرای نگرشهای پایداری محور در بستهبندی در صنعت غذا، ضروری است تا کل چرخه تامین و توزیع به صورت جامع دیده شود. از مرحله تولید و چرخه لجستیک گرفته تا مصرف توسط مصرفکننده. علاوه بر معرفی چرخه بسته بازیافت و استفاده مجدد از بستهبندیهای پلاستیکی، باید به کاهش مصرف پلاستیکها در تولید بستهبندیها همزمان با جایگزینی مواد اولیه نیز فکر کرد. در بحث شیشه و آلومینیوم و تینپلیت همانند بطریهای PET، سیستم عملکردی خوبی برای ایجاد چرخه بسته بازیافت وجود دارد. در آلمان به عنوان مثال، حدود 99درصد از بطریهای PET نوشیدنی با بیعانه بازگردانی، جمعآوری میشوند در حالی که 94درصد از آنها بازیافت میشوند.
در داستانی متفاوت، در مورد بستههای پلاستیکی حتی با وجود اینکه آلمان پیشرو است و پس از آن کشورهای اتریش، بلژیک، اسلووانی در بازیافت پلاستیک با حدود 65درصد قرار دارند اما این محاسبه بر پایه کمیت ضایعات پلاستیکی دریافت شده از مراکز بازیافت است و نه مقدار دقیقی که بازیافت میشود. نسبت قریب به اتفاق ضایعات پلاستیکی تفکیک و تبدیل شده به منابع حرارتی میشوند یا برای دفن به خارج از مرزها فرستاده میشوند. یکی از علتهای مهم برای این موضوع این است که بسیاری از مواد اولیه را هنوزنمیتوان به خوبی جداسازی کرد چراکه مواد بستهبندی مورد استفاده در صنعت غذا از ترکیبهای چندلایه تشکیل شدهاند. این محصولات مزیت بزرگی دارند، با وجود داشتن ورودی مواد کمتر، آنها ویژگی نفوذناپذیری بیشتری دارند که متناسب با خواص خاص هر محصول هستند، همچنین عملکرد محافظتی بسیار بالایی دارند. با این وجود جداسازی مکانیکی این مواد ترکیبی در مقیاس صنعتی، چیزی است که تا به امروز میسر نشده است.
کارهای زیادی برای پیشرفت یا طراحی سیستمهایی برای بازیافت شیمیایی مواد ترکیبی صورت گرفته است. هدف، معرفی سیستم چرخه بستهای است که بتوان با آن مواد پلاستیکی برای استفاده بعدی را بازیافت کرد. بازیافت شیمیایی باعث تجزیه زنجیره مولکولهای پلاستیک به ذرات جداگانه میشود. این تغییر شامل مواردی همچون hydrogenation (تبدیل به هیدروژن)، hydrolysis (هیدولیز آب) و pyrolysis (تجریه در اثر گرما) و در نتیجه بازیابی مواداولیه اصلی برای بستهبندیهای جدید میشود.در مقابل بازیافت زمان و هزینهبر مکانیکی بطریهای PET، به عنوان مثال، عملا تمام پلاستیکها را میتوان با این روش یعنی hydrogenation و pyrolysis و بدون نیاز به جداسازی خیلی پیشرفته بازیافت کرد. اگرچه کار ابتدایی در این زمینه در مراحل آزمایشی قرار دارد و در حال حاضر هیچ جایگزین مناسب و اقتصادی دیگری وجود ندارد.
یک نگرش سازنده دیگر تولید بستههایی است که بر پایه مواد اولیه موجود در چرخه بسته بازیافت انجام میشود. یک مثال خوب از این بحث، بستهبندیهای تولیدشده از فیبر کاغذ هستند چراکه کاغذ را میتوان درون چرخه بسته بازیافت قرار داد و دوباره از آن استفاده کرد. حتی اگر ماده اولیه در سطلهای معمول زباله به جای سطلهای زباله کاغذی ریخته شوند، با روشهایی مدرن در مراکز بازیافت، میتوان آنها را جداسازی کرد و به چرخه بازیافت بسته کاغذ فرستاد.
ارتقا تکمادهایها
نگرش دیگر بهبود و پیشرفت بستههایی است که از مواد تکمادهای (monomaterials) تولید میشوند. این مادهها را میتوان به سادگی در سیستم چرخه بسته بازیافت کرد. در حال حاضر PD و APET مواد اولیه برگزیده برای این هدف هستند. فیلم PP ماده استاندارد پلاستیکی است که بهطور متداول در بستهها مورد استفاده قرار میگیرد. این ماده اولیه به خاطر ویژگی نفوذناپذیری خوب، مقاومت حرارتی و پایداری مناسب مورد توجه است. PP همچنین دارای پایینترین چگالی در میان پلاستیکهای استاندارد است. بستههای تولید شده از PP وزن پایینتری نسبت به سایر مواد دارند که این موضوعی مهم در بحث پایداری و محافظت از محیطزیست است. با این وجود بهکارگیری این ماده اولیه در ماشینهای بستهبندی ترموفرمینگ چالشبرانگیزتر از سایر مواداولیه پلاستیکی است. ماده APET فوق شفاف نیز به خاطر ویژگی ضدعبور بخار آب و گاز نیز مورد توجه قرار دارد. این ماده در مقابل روغن و چربی نیز مقاوم است و میتواند در درجه حرارت 40- تا 70درجه سانتیگراد مورد استفاده قرار گیرد. در حال حاضر بستهها و سینیهای تولیدشده از APET و سایر مواد تک لایه برای بستهبندی مواد غذایی تازه مورد استفاده قرار میگیرند. برای دستیابی به بستهبندیهای قابل اطمینان، وبهای ویژه برای لایه بالایی در نظر گرفته میشوند آن هم به واسطه سیلبندی نازک مانند لاکهای سیل.
هنگام بهکارگیری مواد تکلایه برای مواد غذایی، مهم است که ویژگی نفوذناپذیری آنها را در مقایسه با مواد ترکیبی و چندلایه که تاپیش از این مورد استفاده قرار میگرفت در نظر گرفت. باید یادآور شد که کاهش در لایههای کارکردی، مانند لایه سیل، میتواند برخی پارامترها را تغییر دهد هنگامی که صحبت از پارامترهای فرآیندی میشود.
بایوپلیمرها- جایگزینی کاربردی؟
هنگامی که صحبت از بهبود ماده اولیه برای تولید بستهبندی میشود، موادی که به آنها بایوپلیمر گفته میشود را باید به عنوان یک جایگزین در نظر گرفت. واژه بایوپلیمر شامل دو رده محصول میشود: نخست پلیمرهایی که از مواد جدید تجدیدپذیر تولید میشوند مانند PLA یا PHA. این پلیمرها زیست تخریبپذیر هستند. رده دوم از این مواد آنهایی هستند که از منابع تجدیدپذیر به صورت کامل یا بخشی تولید میشوند که زیست تخریبپذیر به حساب نمیآیند مانند PET یا PE. بر پایه آخرین دانستهها، پلاستیکهای حرارتی PLA کاربردیترین جایگزین برای تولید بستههای ترموفورم تولید شده از بایوپلیمرهای به دست آمده از منابع تجدیدپذیر هستند. با این وجود به خاطر ویژگی نفوذناپذیری و مقاومت پایینشان، کاربرد بستههای ترموفورم تولید شده از این مواد بسیار محدود است. از این مواد اغلب برای بخش میوههای تازه و سبزی استفاده میشود.
چنانچه کسی بخواهد در مجموع بایوپلیمرها را ارزیابی کند، مهم است که تنها جنبههای اقتصادی آن (قیمت و در دسترس بودن) را در نظر نگیرد بلکه بازیافتپذیری این مواد را در انتهای چرخه زندگیمان را هم به حساب آورد. در نبود آموزش مصرفکننده راجع به این مواد اولیه و همچنین فقدان سیستمهای دفن یکپارچه، چندان عملی نیست که بتوان انواع مختلف بایوپلیمرها را از هم جداسازی کرد.
این موضوع میتواند موقعیتی ایجاد کند که پلیمرهای زیست تخریبپذیر به درون چرخه بازیافت پلیمرها سنتی وارد شوند به جای اینکه وارد کارخانههای کامپوست صنعتی شوند.
چالشهای حال حاضر
قوانین جدید بستهبندی به گونهای هدفگذاری شدهاند که بازیافتپذیری بستههای پلاستیکی را بالا ببرند و نرخ بازیافت در مواد اولیه بستهبندی را افزایش دهند. این اهداف صرفا با تعیین سهمیه دستیابی نمیشوند. صحبت بیشتر راجع به خلق مشوقهای مناسب و چهارچوب برای کل صنعت است که بحث بازیافت هم در آن مطرح باشد. چالش دیگر تضمین این موضوع است که بهطور مداوم کیفیت بالای بازیافت در دسترس باشد. تنها در این صورت است که بازیافت شدهها را میتوان به مواد جدید باکیفیت تبدیل کرد. چنانچه فرآیند جداسازی مخدوش شود، مواد تشکیلدهندهای همچون رنگدانهها، نرمکنندهها و روانکنندهها در ماده اصلی میتوانند تاثیری موثر بر کیفیت مواد بازیافت شده باقی بگذارند.
در پایان اینکه انسداد ضایعات پلاستیکی از طریق کاهش حجم مواد اولیه بستهبندی، نگرشی بسیار سازنده است. این هدف را میتوان به وسیله نگرش خلاقانه بستهبندی مانند طراحیهای عالی یا بهکارگیری فناوری جدیدی در ماشینآلات در تولید بستهها به دست آورد. این روشها به طرز موثری باعث کاهش مصرف مواد اولیه و بهبود راندمان آنها خواهد شد.