Bosch is presenting a dual-lane version of the Two-in-One biscuit packing system at interpack 2017. The single-lane system was premiered at interpack 2014 and is already used by customers worldwide. The new high- performance system goes even further in terms of flexibility and speed: it is the first system to produce single, pile and slug packs on two independently operating lanes. Ground-breaking technology teams with robust design and harmonized processes to ensure a high level of overall equipment effectiveness. “The development of the Two-in-One biscuit packing system builds on our existing market success. Our compact system stands for maximum efficiency and productivity, from product distribution to the closed carton”, says Daniel Bossel, product manager at Bosch Packaging Technology.
Intelligent solutions for maximum performance
The distribution station is the first of many innovations. The new Sigpack DHRG reliably forms up to 400 rows of round, oval or square-shaped biscuits per minute which can be fed in a sorted or unsorted way. This innovative solution ensures gentle and flexible handling of the product. Two lanes transport the biscuits flat to the new flow wrapper Sigpack HMAD’s dual sealing station, ensuring extremely gentle handling. The Sigpack HMAD stands out due to its high speed in heat or cold sealing. The heat sealing process reaches film speeds of up to 90 meters per minute and up to 150 meters per minute in the cold sealing process. This advanced system solution also enables fast and flexible format changes. The two lanes can package up to 2,400 biscuits per minute. Manufacturers can configure each lane to produce different packaging formats in varying batch sizes.
The Sigpack PMI infeed module is also new to our portfolio but will not be displayed at interpack. As the link between flow wrapper and cartoner, it merges the flow of products from two into one lane. Each product can be controlled and positioned individually thanks to linear motor technology. The technology is highly adaptable without using vacuum. The Sigpack TTM cartoner allows for quick, reproducible and tool-free format changes. A vertical restart only takes a few minutes to complete. With an output of up to 150 boxes per minute, the toploader guarantees high overall performance on compact footprint.
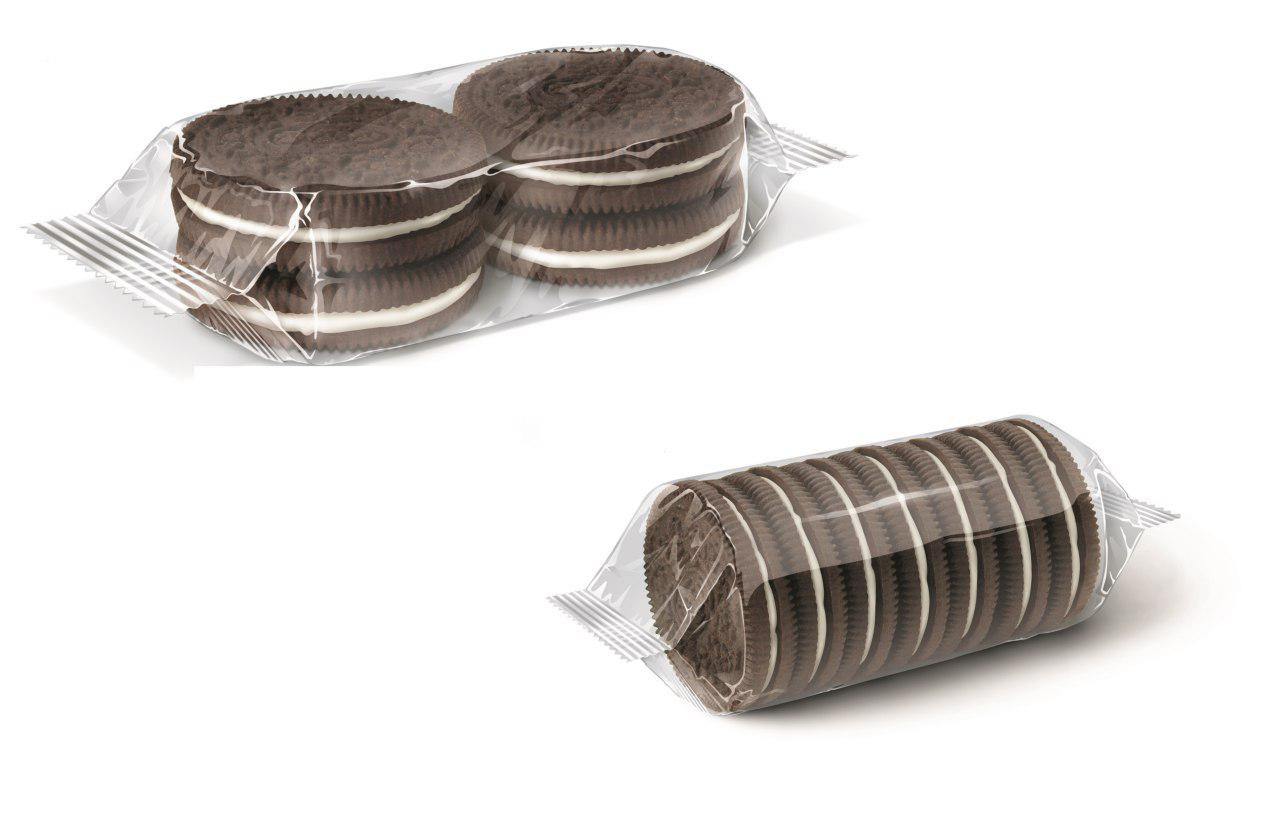
Easy to use and gentle handling of products
The system was designed with ease of use in mind. All the components are seamlessly integrated into the HMI user interface and follow standardized processes. The two lanes can be cleaned and adjusted independently of one another, meaning that production does not need to be halted at any time. The novel design of the product-conveyance system, which works without guide profiles and baffles, means the biscuits are subject to less mechanical pressure than in traditional solutions, thereby guaranteeing a high level of quality overall.
New industry 4.0 solutions increase efficiency, productivity and quality
The Industry 4.0 solutions from Bosch support the production process and increase productivity. The biscuit system can be fitted with the Line Dashboard, which gives operators a transparent system overview and detailed information of the complete system status, as well as an easy drilldown to single machines. The Line Dashboard is accessible from each connected HMI 4.0, tablet, Shopfloor Dashboard and PC in the network. Notifications, such as error alerts, can be sent to other HMIs and mobile devices in real-time. This enables operators to react quickly and initiate countermeasures, reducing walking distances and machine downtime. In addition, the Line Dashboard can be used to check individual machines or complete lines, including pre-defined reports and KPIs in real-time, for instance before a shift or operator change.