صنعت کانورتینگ تأثیرات مثبتی بر طبیعت داشته است با توسعه فناوری هایی برای کاهش مصرف انرژی در چرخه بسته بندی، کاهش کلی کربن و زباله های محصولات غذایی (بزرگترین عامل زباله های جامد شهری)، همچنین بهبود بهداشت و در نهایت کاهش هزینه های کلی.از طرف دیگر، صنعت ما برای بهبود در زمینه پایان عمر محصولات کانورت شده، استفاده زیاد از انرژی و انتشار گازهای گلخانه ای مرتبط با فرآیندهای تولید، فضای کافی دارد. توجه به توسعه فناوریهای بهتر و پایدارتر در صنعت ما شامل توسعه ترکیبات کانورت شده است که امکان بازیافت بیشتر را فراهم میکنند، مانند ساختارهای تک ماده ای، ترکیباتی که به دلیل ساخته شدن از یک پلیمر واحد ، با درصد بسیار بالا قابل بازیافت هستند.
دکتر Giancarlo Caimmi / مدیر بازرگانی شرکت Nordmeccanica Group
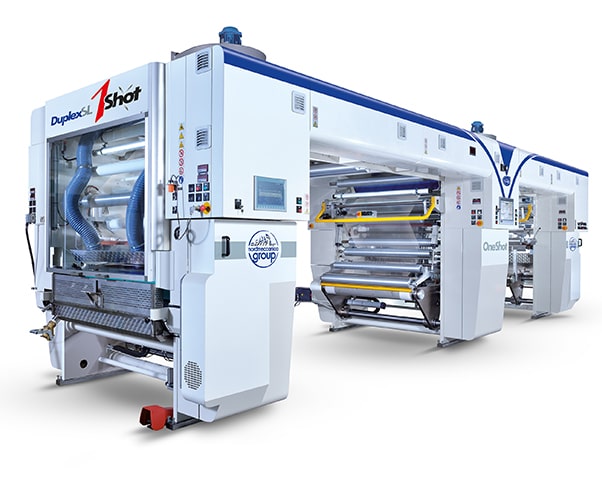
در حال حاضر، هر عضو زنجیره ارزش در حال مشارکت در ایجاد پیشرفتهای جدید است. تبدیل سوبستراهای نوآورانه نیازمند آن است که بخش ماشینآلات زنجیره ارزش، بهویژه در بخش کنترل وب، فناوریهای مناسبی را تنظیم کند. به طور مشابه، توسعه پوششهای کاربردی جدید نیازمند ارزیابی فناوریهای پوششدهی مناسب، انتخاب و توسعه فناوریهای نوآورانه است.
شرکت سازنده ماشین آلات، مسوولیت ارایه راهکارهای سختافزاری کارآمد و متناسب با نیازهای مواد نوین را بر عهده دارد. این امر در روکش زنی و لمینیشن بسیار حیاتی است، زیرا این نوع ماشینها به ویژه تحت تأثیر مصرف انرژی و انتشار آلایندههای آلی فرار (VOCs) قرار دارند.
یک فضای بزرگ برای نوآوری وجود دارد که به طور انحصاری به تولیدکننده ماشینآلات اختصاص یافته است. منظور من بهبود بهرهوری انرژی در فرآیند تولید است. تجهیزات درگیر در فرآیند کانورتینگ، مناسب برای تکامل و کمک به پایداری چرخه تولید هستند. ردپای کربن مرتبط با فرآیند تبدیل، با اجرای برخی نوآوریها و راهکارهای طراحی، میتواند به طور قابل توجهی کاهش یابد.
راهکارهای فنی که در ماشین آلات پوشش دهی و لمینیت پیاده سازی شده اند، عمدتا بر بهره وری انرژی و کاهش انتشار متمرکز هستند. انرژی به طور عمده در فرآیند تبدیل به دو شکل استفاده می شود: برق و گرما. برای تغذیه موتورها، دستگاهها و تجهیزات جانبی مورد نیاز در فرایند، به برق نیاز است. مصرف حرارت در ارتباط است با نیازهای تکنولوژیکی مرتبط با فرآیندهای پردازش، مقررات حرارتی در طول فرآیند و سیستم های خشک کن.
کاهش مصرف انرژی الکتریکی می تواند ابتدا از طریق طراحی هوشمند توسط تولید کننده تجهیزات اصلی (OEM) مورد توجه قرار گیرد. ابعاد و اندازه تجهیزات اهمیت دارد. مسیر وب طولانیتر از حد نیاز، به پایداری غیرفعال کمک میکند و در نتیجه نیاز به استفاده از موتورهای بزرگتر را به همراه دارد که با افزایش نسبی مصرف انرژی همراه است.
یک پیشرفت قابل توجه دیگر، بهرهگیری از اجزای مکانیکی با کمترین اینرسی غیرفعال است. یاتاقانهای کم اصطکاک، تسمههای تایمینگ با راندمان بالا و چرخدندهها، مصرف انرژی را کاهش میدهند. در مسیر حرکت رول مواد (وب) در دستگاه پوششدهی یا لمینت، تعداد زیادی رول نگهدارندهی وب وجود دارد. هر غلتک هرزگرد چندین گرم به اینرسی غیرفعال کمک می کند. هنگامی که ده ها غلتک هرزگرد درگیر هستند، رسیدن به سطح اینرسی غیرفعال در اندازه چندین پوند آسان است.
برای کنترل اینرسی (به معنای مقاومت یک سیستم در برابر تغییر وضعیت آن است. ) بالاتر، نیاز به توان بیشتری داریم. قطعات کم اینرسی، به وضوح گرانتر از قطعات معمولی هستند، اما بازگشت سرمایه آنها سریع است. این موضوعی مهم است که باید هنگام سرمایهگذاری مورد بررسی قرار گیرد. ماشینآلات خوب، این راهکارها را به عنوان یک استاندارد در خود دارند. مزیت این راهکارها، در طول چرخه عمر تجهیزات، قابل توجه خواهد بود. الکترونیک مدرن راه حل های انرژی کارآمدی را ارایه می دهد. کلاس های متعددی از راندمان انرژی در دسترس هستند و این جنبه دیگری است که نباید نادیده گرفته شود. تولید همزمان برق در طول فرآیند تولید، یک فناوری بسیار مهم است که باید به آن توجه ویژه شود. این فناوری درایوهای AC بازیابی کننده است که شامل تبدیل انرژی جنبشی موتور و بار متصل به آن به انرژی الکتریکی می شود.
تمام تجهیزات مدرن با استفاده از موتورها به عنوان ترمز در زمان باز شدن رول طراحی شده اند. استفاده از موتورها به دلیل دقت بالاتر ارایه شده در کنترل حرکت رول توجیه می شود. در بیشتر زمان عملکرد، این موتورها در واقع به عنوان ترمز عمل می کنند. این مرحله ای است که در آن درایو احیاکننده، انرژی جنبشی موتور-بار مرکب (در واقع رول باز شده) را به انرژی الکتریکی تبدیل یا بازسازی می کند. و آن انرژی، در پیشرفتهترین سیستمها، برای تغذیه موتورهای ماشینهای دیگر در مواقعی که تقاضا بیشتر است، استفاده میشود.
مزیت این فرآیند این است که حدود ۲۰ تا ۲۵ درصد از انرژی الکتریکی مصرفی توسط تجهیزات، خود تولید می شود. یک بار دیگر، یک راه حل فنی که به سرعت بازدهی دارد و در طول عمر کل دستگاه صرفه جویی ایجاد می کند. طراحی ماشین میتواند به طور قابل توجهی بر کاهش انتشار آلایندهها و بهبود پایداری تأثیرگذار باشد.
پوشش و لمینت شامل چندین فناوری مورد استفاده در این صنعت است: چسب های بدون حلال؛ ترکیبات چسب خشک؛ ترکیبات چسب مرطوب؛ ترکیبات پخت شده با انرژی؛ ترموپلاستیک ها… . رده چسب های بدون حلال نیازی به خشک شدن ندارند، در نتیجه هیچ گونه انتشار VOC وجود ندارد. هوایی که به دلایل ایمنی در سر کوتر خارج می شود و شامل ” part per billion ” مونومر است، توسط اکثر مقررات به عنوان هوای پاک در نظر گرفته می شود.
این دلیل رشد استفاده از لمینت بدون حلال در همه زمینه ها است. یک لمیناتور بدون حلال در مقایسه با یک لمیناتور مرطوب یا خشک می تواند تا 80 درصد در مصرف انرژی صرفه جویی کند. در فرآیندهای اتصال مرطوب و خشک، دستاوردهای افزایش بازدهی عمدتا به طراحی کوره مربوط می شود، که کوره های هوای گرم رایج ترین راه حل هستند. هوا در دمای فرآیند گرم می شود و سپس انرژی همراه با هوا باید به ترکیب پوشش داده شده منتقل شود تا در حین فرآیند خشک شدن، آب یا حلال ها از آن خارج شوند.
در اینجا، راندمان فرآیند خشک کردن به طراحی فر مرتبط است. هرچه هوای گرم بیشتر مجبور شود با ترکیب پوشش داده شده (عمدتا از طریق آشفتگی اجباری) در تماس باقی بماند، راندمان انتقال حرارت بالاتر خواهد بود. به این ترتیب فرآیند خشک کردن تسریع میشود و میتوان طول فر را با مزایایی در کار با وب کاهش داد. همانند هر فرآیند مرتبط با گرما، عایق حرارتی کلید کارایی است. یک کوره خشک کن می تواند مقدار زیادی انرژی را از طریق تابش و جابجایی به بیرون منتشر کند. عایق حرارتی سهم قابل توجهی خواهد داشت.
چرخش مجدد هوای داخل فر نیز در افزایش راندمان موثر است. اجبار بخشی از هوای تخلیه شده به گردش مجدد به سمت فر با درصدهای کنترل شده، امکان صرفه جویی قابل توجهی در انرژی را فراهم می کند. مبدل حرارتی پایین دست کوره نیز راندمان را افزایش می دهد. استفاده از انرژی بازیابی شده برای کاربردهای ثانویه تقریبا برای مبدل رایگان خواهد بود. هزینههای مرتبط همیشه خیلی سریع بازپرداخت میشوند. در هر فرآیندی که به مقدار قابل توجهی انرژی حرارتی برای کنترل فرآیند نیاز دارد، طراحی ماشین تأثیر قابل توجهی دارد. هرچه انتقال انرژی کارآمدتر باشد، مصرف انرژی و هزینههای مرتبط با آن کمتر خواهد بود.
در ترموپلاستیکها، عایق حرارتی نقش بسیار مهمی ایفا میکند. در ماشینآلات تبدیل این مواد، کنترلهای حرارتی در هر مرحله از فرآیند- از مرحله ذوب شروع شده و با فرآیند پوششدهی و غلتک خنککننده ادامه مییابد- استفاده میشوند. اگر دستگاه عایق بندی نداشته باشد، پراکندگی حرارتی در همه جا رخ خواهد داد.
سرمایه گذاری در سخت افزار جدید و بهبود بهره وری انرژی در تجهیزات موجود از طریق تجزیه و تحلیل مصرف انرژی و اجرای راه حل های مناسب، هم به محیط زیست کمک می کند و هم صرفه جویی قابل توجهی در هزینه ها برای مبدل ها به همراه دارد. تجهیزات مهندسی شده مناسب در مقایسه با گزینه های پایه ای ممکن است صرفه جویی انرژی تا 50 درصد یا بیشتر را نشان دهند. این نه تنها به معنای بازگشت سرمایه سریعتر است، بلکه در طول کل عمر تجهیزات صرفه جویی ایجاد می کند.